Maszkgyártó nagyhatalom lehetünk egy magyar technológiának köszönhetően
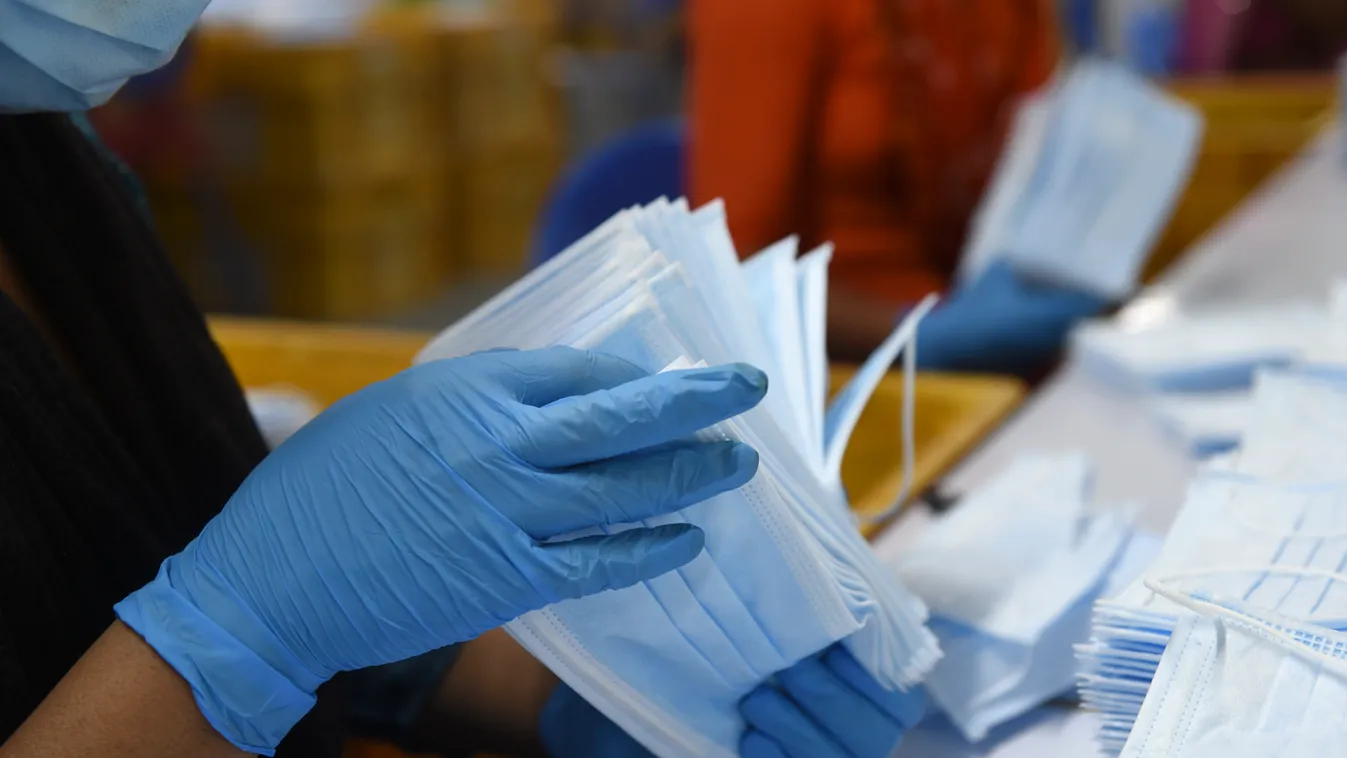
Honnan jött az az elképzelés, hogy védőmaszk gyártásba fogjanak, és az ehhez kifejlesztett technológia miért tekinthető egyedinek?
Amikor márciusban elérte Magyarországot a COVID-19 járvány, idehaza is hirtelen megugrott a védőmaszkok iránti tömeges kereslet. A külföldi beszerzések egyrészt bizonyos kiszolgáltatottságot teremthetnek, mert számos ország, amely rendelkezik megfelelő gyártási kapacitással, érthető okokból elsősorban a saját polgárai védelmére koncentrál, és csak az ezt meghaladó feleslegét exportálja, amire pedig sok jelentkező lehet.
Különösen kritikus pont a maszkok gyártásához szükséges alapanyag beszerzése, mert ez határozza meg a gyártási kapacitást is. A maszknagyhatalomnak számító Kína éppen a miatt vált világszerte első számú beszerzési forrássá, mert egyszerre állítja elő az alapanyagot, valamint a készterméket is.
Innen jött az ötlet, hogy a magyar mérnöki tudást, leleményt és technológiai kreativitást ötvözve
egy olyan, teljesen komplett technológiai rendszert építsünk ki,
amely az alapanyag előállításától kezdve a WHO ajánlásának és a legmagasabb biztonsági követelményeknek megfelelő maszk gyártásán, a késztermék sterilizálásán és csomagolásán át az egész gyártási műveletet egyetlen folyamatban egyesíti olyan mennyiségi kapacitással, ami még egy erős járvány esetén is könnyedén és folyamatosan fedezni tudja a hazai igényeket.
Hogyan fogtak hozzá mindennek a megvalósításához, és ehhez milyen technológiai háttér kiépítése vált szükségessé?
Legelőször azt próbáltuk felmérni, van-e az elképzelésünkre itthoni igény. Küldtünk egy előzetes témavázlatot az államnak, konkrétan megkerestük a Belügyminisztériumot, a járvány elleni védekezés központi irányítóját, ahonnan alig egy nappal később pozitív visszajelzést kaptunk.
Természetesen kíváncsiak voltak arra, hogy annak a kivitelezéséhez amit felvázoltunk, megvan-e a kellő szakértelmünk. A hazai tulajdonú METRIS-3D Kft.-nek már húszéves gyakorlata van a gyártástervezésben és ellenőrzésben, ami ehhez is biztosítja a megfelelő szellemi tőkét.
Ezért projektcégként létrehoztuk a ViroGear Kft.-t, és összeverbuváltuk a hazai mérnök-elitet.
A kiváló szellemi holdudvarnak köszönhetően mindössze négy hónap alatt sikerült eljutnunk a megvalósításig,
és már most jelentős külföldi előrendelésekkel rendelkezünk többek között Szlovéniából, Németországból, Szlovákiából és Oroszországból.
De természetesen számunkra Magyarország az első,
hiszen azért vágtunk bele a projektbe, hogy elsősorban a hazánknak használjunk. Az általunk kifejlesztett tíz gyártósorral bármilyen járvány tetőzése idején is képesek lennénk a teljes hazai szükséglet folyamatos biztosítására.
Ez praktikusan milyen kapacitást jelent például a gyártási darabszámban?
Az általunk kifejlesztett gyártósor napi 50 ezer maszkot képes előállítani, havonta pedig 1,5 milliót. Ez az érték értelemszerűen egyetlen gyártósorra vonatkozik, tehát mind a tíz üzembe állítása esetén ezek a számok is megtízszereződnek.
A gyártósorral az FFP2-es kategóriába tartozó szűrőképességű maszkokat tudunk előállítani. Az FFP2 az Egészségügyi Világszervezet, a WHO által kifejezetten ajánlott,
és a legmagasabb védettséget jelentő szűrőképességgel rendelkező maszktípus,
amely más maszkokkal szemben nem csak a viselőjét, hanem a környezetét is védi.
Fontos hangsúlyozni, hogy ez pillanatnyilag megfelel a legmagasabb szintű elvárásoknak is.
A kormány a Budapesti Műszaki és Gazdasági Egyetemet jelölte ki a ViroGear-maszkok megfelelőségi vizsgálatára, a fejlesztés támogatásába pedig az ITM és a Pénzügyminisztérium is beszállt.
De miért fontos a folyamatos ellátás, pontosabban, mit mutatnak az egészségügyi-tudományos tapasztalatok a maszkok védelmi képességével kapcsolatban?
A folyamatos gyártás a biztonság, vagyis a maszkok előírásszerű rendszeres cserélhetősége miatt fontos. Például a legjobban elterjedt úgynevezett orvosi vagy sebészi maszk,
a BFE-95 típus csak a környezetét, de a viselőjét nem védi.
Nagyon sokan nincsenek is tisztában azzal, hogy ezt a maszktípust három órás használat után el kell dobni, mert már nem biztosítja tovább a védettséget.
Ezzel szemben az általunk kifejlesztett maszk védelmi ideje tíz óra, és nem csak a környezetet, hanem a viselőjét is védi, arról nem is beszélve,
hogy az elvégzett tesztek szerint minden más maszknál komfortosabb és sokkal könnyebb benne a légzés,
mert nagy hangsúlyt fektetünk az anatómiai illetve ergonómiai formatervezésre. A mi maszkunk ultrahangos hegesztéssel készül, ezért teljesen zárt, szemben a varrott maszkokkal, amelyeknél a tű ütötte lyukak miatt nem teljesen tökéletes a zárás.
A dolgok jelenlegi állása szerint mikor kezdődhetne el a hazai gyártás, és ehhez még mire lenne szükség? És mitől számít különlegesnek az önök által kifejlesztett technológia?
Terveink szerint augusztus második felében elkezdhetjük a hazai gyártást. A gyártási kapacitást igen rugalmasan a mindenkori aktuális igényekhez tudjuk hozzáigazítani,
és a hazai beszállítók segítségével gyakorlatilag bármilyen igényt ki tudunk elégíteni,
sőt, a kapacitásaink lehetővé tennék az európai igények egy jelentős részének a lefedését is.
Amitől a gyártási rendszerünk jelenleg európai viszonylatban is egyedülállónak számít az az, hogy rendelkezünk külön alapanyag gyártó sorral, ami naponta két tonna Melt-Blown típusú alapanyagot – az összes egészségügyi maszk alapanyagát – képes előállítani.
Szemléltetésként: a napi kettő tonna legyártott alapanyag hárommillió maszk előállítására alkalmas.
Ez az alapanyaggyártó sorunk összesen 60 maszkgyártó sor egyidejű ellátására képes. Tehát ez az innovatív magyar technológia potenciálisan akár egész Európa ellátására is alkalmas kapacitássá fejleszthető.